Saws Making, like many other industries has it's own jargon, which as far as I am aware has been sparsely documented over the years, so in order to provide a consistent framework for discussion and research, I am presenting here a starting point, to which others can refer so that we can all agree on what that thing, you know the bump just above the whatsit, what's that called again! If you have a different name for something listed here let me know about it.
The subject of nomenclature is fraught with inconsistencies, local variations, colloquial usage, traditional usage, words invented to cover specific features and so on. It is my intention, to provide a starting point, so that we can have a common language for research and discussion. I am aware that words like "split nuts" are probably a late addition to the jargon, and would perhaps not have been understood by a 19th Century sawmaker. But, the term has gained currency through usage. And the current usage is what I am attempting to document.Research into the etymology and historic usage may provide a more complete lexicon over time.
Saws come in a bewildering array of various sizes, different tooth patterns and pitch etc. See end of this article for some more information on names of different saw types.
Starting with the basics.
The Basic Handsaw.
Saw image from "Sheffield Trade List of Prices 1889 Edition"
Nomenclature (with additions) from R.A.Salaman "Dictionary of Woodworking Tools"
(Keywords:Nib,Toe,Rip,Cross-Cut,Breasted,Taper,TaperGround,Etch,Heel,Medallion,Handle,Tote,Skew Back)
Ok, so if someone says they have a straight backed handsaw with eagle medallion and split nuts, slightly breasted, with intact nib, you will know exactly what they are on about. Also note that some early saws are stamped rather than etched. Whatever you do, never never ask what the nib is for, not if you value your sanity.
No moving on, my favourite
The Backsaw.
Saw image from "Sheffield Trade List of Prices 1889 Edition"
Nomenclature from various sources, Thanks to Tim Corbett - Gramercy Tools for "Canted"
(Keywords: Cant,Canted,Canting,Toe,Etch,Heel,Medallion,Screws,Split Nuts,Handle,Tote,Back,Stamp,Makers Mark)
Now, you can start to really pretend you know about saws, just say it's an open handled dovetail saw with brass back with 1/2" cant and R.Groves and Sons Trademark. With "USE" Medallion and split nuts with a beech handle. (better than saying, it's a short little saw with a funny looking handle)
Now we move into more advanced territory, starting with the Handles... First up the Closed Handsaw Handle. Fishtail or Dolphin Pattern.
The Dolphin Pattern Closed Handle
Saw image from "Sheffield Trade List of Prices 1889 Edition" digitally modified
Nomenclature from various sources, notably Philip W Baker
(Keywords: Cheek,Lamb's Tongue,Lower Ogee,Chamfer,Beak,Recurve,Bottom Horn,Top Horn,Fishtail,Dolphin,Base Nib)
Now we come to a variation on the closed handle called the London Pattern, this one has a flat bottom, rather than the "fishtail" or "dolphin" pattern.
This one however is a backsaw handle, rather than a handsaw. The grip position is higher up and more angled, but we'll get to that in a later article.
The London Pattern Closed Handle
Saw image from "Sheffield Trade List of Prices 1889 Edition" digitally modified
Nomenclature from various sources, notably Philip W Baker
(Keywords: Cheek,Lamb's Tongue,Lower Ogee,Chamfer,Beak,Recurve,Bottom Horn,Top Horn,Fishtail,Dolphin,London Flat, Top Nib)
The open handled dovetail saw with a handle tailored to suit your own hand can be a joy to hold and a delight to use, and possibly the most elegant of all the saw handles.
The Open Handle
Saw image from "Sheffield Trade List of Prices 1889 Edition"
(Keywords: Cheek, ,Lower Ogee,Chamfer,Beak,Recurve,Bottom Horn,Top Horn,Fishtail,Dolphin,London Flat, Top Nib)
Saw Tooth Nomenclature
The components of a saw tooth are the face, the point or tip, the back of the tooth, and the gullet, teeth that we will consider here are standard rip and cross cut teeth, but be aware there are many other tooth patterns and variations, from Japanese pull saws to large 2 man cross cut saws. The main variables we have to define for handsaws are the pitch (how many points per inch), the rake, set, and fleam, standard gullets are constrained by the triangular (60 degree) saw files. So this is just the basics you should know for handsaws. First off the simplest is the rip saw.
The Rip Saw Tooth Pattern.
(Keywords: Gullet, Rake, Set,Kerf,Tooth)
Next, we look at the rip saws more complicated brother the cross cut saw, the main difference here is that the teeth are filed at an angle to the blade, that angle is called the "fleam angle"
The Cross Cut Tooth Pattern.
(Keywords: Gullet, Rake, Set,Kerf,Tooth,Fleam)
Choice of PPI, rake, fleam and set are dependant on whether you are cutting hard or soft timber, how thick and so on, a discussion of those choices is not within the scope of this document. Here we just tell you the names. (it is about nomenclature after all).
Now let's fill in a few gaps, the names for handsaws of various types, has changed over the years, let's look back and see what names were used in 19th Century Britain. That's what we are interested in after all.
The most often quoted authority for naming the different saw types is Holtzapffel (London 1846) so let's have a look at that first.
Name | Length | Width at heel | Width at Toe | Points Per Inch |
Rip Saw | 28 - 30 | 7 - 9 | 3 - 4 | 3 1/2 |
Half Rip Saw | 26 - 28 | 6 - 8 | 3 - 3 1/2 | 4 |
Hand Saw | 22 - 26 | 5 - 7 1/2 | 2 1/2 - 3 | 5 |
Fine Hand Saw | 22 - 26 | 5 - 7 1/2 | 2 1/2 - 3 | 6 |
Panel Saw | 20 - 24 | 4 1/2 - 7 1/2 | 2 - 2 1/2 | 7 |
Chest Saw | 10 - 20 | 2 1/2 - 3 1/2 | 1 1/4 - 2 | 6-8 |
Table Saw | 18 - 26 | 1 3/4 - 2 1/4 | 1 - 1 1/2 | 7-8 |
Compass Saw | 8 - 18 | 1- 1/2 | 1/2 - 3/4 | 8-9 |
Key Hole Saw | 6 - 12 | 1/2 - 3/4 | 1/8 - 1/4 | 9-10 |
Pruning Saw | 10 - 24 | 2 - 3 1/2 | 1/2 - 1 1/4 | 4 -7 |
Table of Backsaw Names and Sizes
Name | Length | Width |
Points per Inch |
|
Tenon |
16 - 20 |
3 1/4 - 4 |
10 | |
Sash | 14 - 16 |
2 1/2 - 3 1/4 |
11 | |
Carcase | 10 - 14 |
2 - 2 1/2 |
12 | |
Dovetail | 6 - 10 |
1 1/2 - 2 |
14 - 18 |
Compiled from R.A.Salaman "Dictionary of Woodworking Tools"
It will be immediately obvious that the names of many saws have changed since 1846, there are some that have dissapeared from general usage and some where the name has changed from earlier usage. Today's tenon saw for example is more like a carcase saw from the 19th Century. Whereas a 19th Century tenon saw would be called a mitre box saw today.
I will edit and add to this periodically, so check back every so often. Think of this as a first draft.
Ray Gardiner 2008
Many thanks to Peter Evans, The Tradional Tools Group (Sydney) for making this list available.
Some References on Saws and Saw Sharpening --- Compiled for The Traditional Tools Group Inc by Peter Evans
The Web is a growing source of information – and disinformation. A good start is:
vintagesaws.com/library/primer/sharp.html, this includes references, and is a good primer on saw sharpening
geocities.com/plybench/shop_projects.html and
geocities.com/plybench/saw_sharpen.html, some useful information.
members.cox.net/wcrittner/sharppage.htm, a beginner’s experiences
http://www3.telus.net/BrentBeach/sawjig/index.htm Brent Beach is obsessive on sharpening, would probably take you a few hours to fully explore his web site. This is a detailed guide to his approachl
norsewoodsmith.com, a lot of information on saws and sharpening, excellent
members.brandx.net/free/websites/bbrode/woodwork/sharp.html had a good primer on sharpening, and covers other issues of saw refurbishment
wkfinetools.com has many references including a lot of Disston material, rather than the specific web addresses below you are probably better off starting at the home address.
oldtoolsshop.com/index.asp; note the specific references below, may be better to access through the home page, rather than type in a long address
disstonianinstitute.com provides an in-depth look at Disston saws and has extracts from a number of Disston publications.
[if you see something you like on a website, download it because either the material or the site may not be there tomorrow]
Books:
Currently in Print:
Keeping the Cutting Edge: Setting and Sharpening Hand and Power Saws, Payson, Harold H., Wooden Boat Publications, 1988
The Complete Guide to Sharpening Leonard Lee
Classic Hand Tools by Garrett Hack, chapter 10
The Handsaw Catalog Collection – A compilation from the following catalogues E.C. Atkins & Co. of Indianapolis 1919, Henry Disston & Sons of Philadelphia 1918, Simonds Manufacturing Co. of Fitchburg, Mass. 1910, and Spear & Jackson of Sheffield, England 1915, Astragal Press 1994, 136 pp
Henry Disston & Sons Company General Line Catalog 1876, Henry Disston & Sons Company. 86 pp (reprint)
Simonds Saw Mfr. Co. General Line Catalog, Simonds Saw Mfr. Co., 195pp (reprint)
Patented American Saw Sets, An illustrated patent directory 1812-1925, 2nd ed, Todd L. Friberg, Osage Press
Hand-saw Makers of North America, Schaffer, L. Erwin, 1999, Osage Press
Hand-Saw Makers Of Britain: A Checklist Of Hand-Saw Makers, Schaffer, Erwin L. and Don McConnell, Osage Press, 151pp
Saws & Sawing, Ian Bradley (Workshop Practice Series), Trans-Atlantic Publications, 1986, 96pp
Saga Of The Saw Filer, Holbrook, Armstrong Mfg. Co. 2006 (1st publ 1952), 45pp
Saw Filer’s Handbook, PS Quelch, Armstrong Mfg. Co. 2006 (reprint), 130pp
Out of Print (where available on-line as PDF files, the web location of the file is noted):
Toolmera Collection of Books on Sharpening (Downloadable PDF's)
Toolmera Collection of Trade Catalogues (Downloadable PDF's)
Disston
A good selection of Disston Literature can be found at:-
http://www.wkfinetools.com/hUS/saws/Disston/pubs/index.asp
The Saw in History, published by Disston, many editions up to at least 9th in 1978, 4th in 1916,
http://www.wkfinetools.com/hUS/saws/Disston/pubs/pg/1916-TheSawInHistory.asp
also available at http://www.archive.org/details/sawinhistory00henrrich
Disston Saw, Tool and File Manual, Henry Disston & Sons, many editions until 1955. A number of editions at
http://www.wkfinetools.com/hUS/saws/Disston/pubs/index.asp
The Hand Saw, how to use it, how to choose it, how to keep it, Henry Disston & Sons, 1st edition 1876, last edition 1955 (by which time Disston was a subsidiary of HK Porter), a number of editions available at http://www.wkfinetools.com/hUS/saws/Disston/pubs/1875-TheHand-Saw/1875-TheHand-Saw.asp
and also at:- oldtoolsshop.com/storageBin/index.asp
Disston Tool Manual For School Shops A Book of Practical Information on the Construction, Use and Care of Saws, Tools, and Files, Disston, many editions beginning 1927
http://www.archive.org/details/disstonlumberman00henrrich
Disston Lumberman's - Containing a Treatise on the Construction of Saws and How to Keep Them in Order, Disston, 1st edition 1888 and many later editions until ?, the 1902 edition reprinted by Astragal Press in 1994. the illustration is the cover of a booklet (probably WW2 period of an extract from the Lumberman title.
Disston Handbook on Saws, Disston, 1st edition 1907, and several later editions. 1914 and 1919 editions available at
http://www.wkfinetools.com/hUS/saws/Disston/04pubs/pg/1914-HandbookOnSaws.asp
also the 1912 edition is at http://rosetools.bizland.com/id66.html
Disston Catalogues, many editions, including 1876, 1887, 1906, 1911, 1914, 1920, 1949; 1914 reprinted by Roger Smith in 1976, some extracts from this catalogue are on the web at http://mysite.verizon.net/dastrom/oldtools/disston/toc.htm
THE HAND-SAW. How To Use It, How To Choose It, and How To Keep It, Henry Disston & Sons, 1875, available at
http://www.toolemera.com/Trade%20Catalogs/vintagecatalogst.html
Proper Care of your Hand Saws, Disston Division of HK Porter Australia
The Disston Crucible - A Magazine For The Millman, Disston & Sons; vol III No. 8 September, 1914 is available at:-
http://www.wkfinetools.com/hUS/saws/Disston/pubs/pg/1914-HandbookOnSaws.asp
there were a number of issues up to 1928 at least; they are rare and expensive to acquire; they probably ended up in the furnace when read.
Why a Saw Cuts, F.M. Bassler, Henry Disston & Sons, 1916
The New Line of Disston Handsaws, Henry Disston & Sons, 1928, 21pp, http://www.disstonianinstitute.com/1928brochure.html.
The Pruning Book, Roland B Gilman, Henry Disston & Sons, 1921 and later editions, 105pp
DISSTON saws ∙ tools ∙ files ∙ knives ∙ steel, 1950’s booklet with ads + 22 blank note pages for the tradesman
Disston Illustrated Trade Price Sheet, 1954, shows there is a still a fairly wide range of saws listed, available at
http://www.wkfinetools.com/hUS/saws/Disston/pubs/hD-price1954/index.asp
Carpenter's Notebook, 1950s, brochure with a few pages of saws, plus note sheets for the carpenter to make notes – about timber perhaps? Available at
http://www.wkfinetools.com/hUS/saws/Disston/pubs/1950-CarpNotebook/1950s-HD-carpenterNotebook.asp
Better and More Economical Sawing, Disston Steel - Henry Disston & Sons
The Mysteries of Disston, Disston
Simonds
The cross-cut saw, Simonds Saw and Steel Co, Fitchburg, MA, 1929
The Simonds Saws & Knives, Catalogue No. 19, 1919, reprinted by Roger smith in 1994
There are a number of catalogues over the years; Simonds still exists as a company, but no longer makes hand saws. http://oldtoolsshop.com/z_pdf/1Simonds/1923-SimondsCatalog-HandSaws-ne.pdf
How to file a cross-cut saw, Simonds Saw and Steel Company, 1937
How to File a Hand Saw, Simonds Manufacturing Co
The Professor and the Saw: a Little Story for Those Who Like to Use Tools, Simonds 1915, Pamphlet 47 pp
Hack Saws and How to Use Them, Simonds Saw & Steel Co, 1958, 31pp
Simonds Guide For Carpenters, Simonds Saw & Steel Co, 64pp
Simonds Guide for filers and Sawyers, Simonds Manufacturing
Simonds "The Circular Saw"
http://www.archive.org/details/circularsawguide00simorich
The Care and Use of Circular Saws in Woodworking Plants, Simonds Manufacturing, 1946, 88 pp, available online and also as a reprint archive.org/details/circularsawguide00simorich
The Circular Saw, Simonds
Atkins
Saw Sense, E.C. Atkins & Co, 32pp, available at oldtoolsshop.com/z_pdf/1Atkins/Atkins-SawSense-ne.pdf
E. C. Atkins Silver Steel Saws - Saw Sense, E.C. Atkins & Co, available at oldtoolsshop.com/z_pdf/1Atkins/AtkinsSilverSteelSawSense-ne.pdf
The Atkins Saw Book for Home Craftsmen, E.C. Atkins & Co, 1930, 32pp
Atkins Metal Cutting Saws, Atkins Metal Cutting Hand Saws, Atkins Circular Metal Cutting Saws blades, Hack Saw Blades, Hack Saw Frames Atkins Kwik-kut Power Hack Saw Machines, etc, early 1900s
Saws in the Filing Room, E.C. Atkins & Co, c 1910, 64pp
The Saw Its Ancient and Modern Development, E.C. Atkins & Co, nd
Atkins Catalogs, a number of editions including 1914, 1919, 1928, 1941 (Atkins Saws, Saw Tools, Machine Knives & Files Catalog, 155 pp)
Atkins & Co Saws – Saw Tools Mill Specialities No 18, 1919, E.C. Atkins & Co, 246pp
Atkins Mill Saws, E.C. Atkins & Co, booklet, nd c.1920’s
Atkins Saw Book for the Farm Workshop and Woodlands, 1931, http://www.roseantiquetools.com/id220.html
Other US
Winchester Catalogue 1923, http://www.roseantiquetools.com/id220.html
The filers' success, J H Miner, 1915, 24pp
Miner's Manual of Saw Hammering and Filing, J. H. Miner, B.F. Ulmer Company, 1905, 60pp
Spear & Jackson
The story of the saw, P. Jones and E. Simons, 1961, Spear & Jackson, Ltd., Sheffield, 80pp
Concerning Saws, Spear & Jackson Ltd,
Saws, Knives & Tools For Sawmills, Spear & Jackson Ltd, 1924, 58pp
Spear & Jackson Saws and Tools Catalogue No. E7, 1953, 132 pp
Some Hints on the Care and Maintenance of Handsaws, Spear & Jackson Ltd, 1960’s ?, 11pp
Tyzack
Servicing Your Saws. W. Tyzack, Sons & Turner LTD., Sheffield c1950, 20pp
What You Should Know about Handsaws, Sanderson Brothers and Newbould Ltd, Sheffield
The Tyzack Family History Site
http://www.tyzack.net/download.htm
Nicholson
Sawology: A Nicholson handbook, Nicholson File Company, 1959
"---being a brief account of the History, Manufacture, Variety and Uses of saws for the cutting of ferrous and non-ferrous metals, hard plastics and rubber, wood, and other dense materials . . . A useful handbook and guide for the shop superintendent, production foreman, mechanic, or home craftsman."
Australian
Service Manual, Maintenance of Circular Saws, Wiltshire File Co., Melbourne, 20 pp
Service Manual for Maintenance of Handsaws Prepared by the Service Department, The Wiltshire File Co. Pty. Ltd, 20pp
Turner Atkins Quality Saws, Saw-Blade Information, booklet
Early Texts
Saw Dictionary - The Care, Selection and Proper Fitting of Handsaws, Charles Johnson 2nd ed, 1909, 50pp
Saws : their care and treatment, HW Durham, William Rider & Son, London, 1916, 272pp (a US edition in 1917), State Library of NSW S621.93/1
The saw doctor's handbook, Drabble & Sanderson, 1925
Boynton's Improved Patent Lightening Saws. New York, E. M. Boynton, Sole Proprietor And Manufacturer. No. 80 Beekman Street. 1872, 24pp.
HAND SAWS. Their Use, Care and Abuse. How To Select, and How To File Them. ... Fred T. Hodgson. Philadelphia, David McKay, 1888. Available at http://www.toolemera.com/Books%20%26%20Booklets/library-sharpeni.html
SAWS: the history, development, action, classification and comparison of saws of all kinds, by Robert Grimshaw, the 1880 edition reprinted by Astragal Press as Grimshaw on Saws
http://www.archive.org/details/sawshistorydevel00grimrich
Saw Filing and Management of Saws, R. Grimshaw, The Norman Henley Publishing Co., NY, 1912 archive.org/details/sawfilingmanagem00grimrich
The Art of Saw-Filing, scientifically Treated & Explained on Philosophical Principles, H.W. Holly, John Wiley, Y, 1st ed 1864, a number of revised editions, 56pp. Get it at (1882 ed) http://www.toolemera.com/Books%20%26%20Booklets/library-sharpeni.html
Suggestions On The Care Of Saws, By C.C. Taintor: Inventor Of The Taintor Saw Set. Taintor Mfg. Co, NY, 1908, 23pp
Saws and Sawing, by Sydney Lister, 1st edition 1937, Lomax, Erskine & Co., London, 150pp, picture of a later edition 1946 cover
Saw Efficiency, Ohlen-Bishop Saws, Columbus, Ohio, 1937, 60 pp
The Art of Saw Doctoring, Wide Bandsaws, by Arthur Simmonds, 208 pp
Monagen Saw Works Price List, 1860 catalogue reprint 1976, 36 pp
COVEL-HANCHETT Saw and Knife Fitting MANUAL, Covel-Hanchett Co. Big Rapids, Michigan, 1943, 472pp
Magazines
Woodworking magazines occasionally print saw and saw sharpening articles:
Fine Woodworking #68, Sharpening Handsaws, It's a matter of knowing all the angles, Harold H. Payson
Fine Woodworking #39, The Backsaw, How to buy, use and sharpen this basic tool, Ian Kirby
Fine Woodworking #125, Sharpening Handsaws, Make your saws cut straight and fast, Fred Wilder
Fine Woodworking #121, Soup up a Dovetail Saw, Refile teeth and reduce set for better cuts, Mario Rodriguez
Fine Woodworking #183, Sharpening a dovetail saw, Chris Gochnour
Fine Woodworking #22, Sharpening saws, principles; procedures and gadgets, J. Paquin
The Woodworker, 1920 Volume XXIV, Woodworking tools – The Saw, a series of chapters across issues starting at p120.
Many old woodworking texts (few in print, but generally available 2nd hand) have a chapter on saw sharpening; some good ones are:
Audels Carpenters and Builders Guide, many editions, vol 1, ch 15 “Saw Filing” 24pp
The Woodwright’s Companion, Roy Underhill, University of North Carolina Press, 1988
DVD/Video
Hand Saw Sharpening, Tom Law, ALP Productions
Sharpening a Dovetail Saw
Tune up a dull saw to cut fast and straight in five steps, with Chris Gochnour
http://www.taunton.com/finewoodworking/SkillsAndTechniques/SkillsAndTechniquesArticle.aspx?id=24976
A Tool Kit for Sharpening Handsaws, find out which tools are required to revive a dull handsaw with Chris Gochnour taunton.com/finewoodworking/SkillsAndTechniques/SkillsAndTechniquesArticle.aspx?id=24977
The Roy Underhill TV shows for 2006 are now available on the web, whilst the picture is small, they are pretty clear (on high speed). There are bound to be some saw related shows in previous years, hopefully archive shows will become available over time: pbs.org/wws/schedule/26season_video.html. Note that you are not able to download the videos.
------------------------
This is a work in progress; if you see errors in any of the above or have additional material please send it to This email address is being protected from spambots. You need JavaScript enabled to view it., thank you
Additional saw references to 1st version – March 2008
Text Book of Atkins Silver Steel Saws Hand Rip and Panel How to Care for and Use them for Manual Training Schools Mechanics Farmers and all Users of Saws, E.C. Atkins., 1927, 28pp
More information:
The Saw Its Ancient and Modern Development, E.C. Atkins & Co, 1906, 58pp. A history of Atkins in a historical context, published by the Atkins Advertising dept, which probably says it all.
Saws and Sawing Machinery, Eric N. Simons, 1946 [Powerhouse Library]
US forestry Service reference list:
http://www.fhwa.dot.gov/environment/fspubs/04232822/page24.htm
Revision History
Initial check that links were working and prune/update any dead links. Ray 3rd August 2008
Fixed links for changes at wkfinetools. Ray March 2009
Downloadable PDF http://www.backsaw.net/SawHandles101.pdf
This is a tutorial of how to make a saw handle, I will probably refine and update as time goes by, however for anyone embarking on this process for the first time, it's a good idea to first review the existing on-line literature.
The most often quoted reference is Leif Hansen's Backsaw Project at http://norsewoodsmith.com/node/68 I recommend downloading the pdf file as a general reference.
The second one is Tim Hoff's two part How to make a handsaw.
Part 1. http://www.cianperez.com/Wood/WoodDocs/Wood_How_To/INDEX_How_To_pages/TimHoff_MakingSawBlades.htm
Part 2. http://www.cianperez.com/Wood/WoodDocs/Wood_How_To/INDEX_How_To_pages/TimHoff_MakingSawHandles.htm
Tim now has a blog which can be found (the saw handle making part) here:- http://sprucemill.blogspot.com/2008/12/making-saw-handles.html
There are no doubt other tutorials I have missed, if you let me know I will link to them from here.
A good site to also check is http://pedder-altedamenauskiel.blogspot.com/ Look for "Griffbau"=Handle Maker in the links section.
Here are the links...
Derek Cohen http://www.inthewoodshop.com/ShopMadeTools/Small%20Tenon%20Saw.html
Philly Edward http://www.philsville.co.uk/sawhandles.htm
Alice Frampton http://www.leevalley.com/newsletters/Woodworking/1/5/article3.htm
Alan DuBoff http://traditionaltoolworks.com/making-saws/
Mike Wenzloff http://wenzloffandsons.com/saws/kits/index.html
Thanks Pedder for the links.
This is part one of a multipart series that will cover making the back, making the handle and sharpening. The first part is making the handle. A downloadable pdf of the handle making process (much the same as this page) can be obtained from http://www.backsaw.net/SawHandles101.pdf
I bought my split nuts from Mike Wenzloff http://www.wenzloffandsons.com but you could make your own from 3/16 threaded brass rod and 1/2 brass rod, using Leif's "Poor Boy Split Nuts" from here.. http://www.norsewoodsmith.com/node/108
Personally, I love the split nuts from Mike, they are a work of art in themselves.
Now we have reviewed the available literature, it's time to get started. You want to choose a timber that is close grained and durable, among the traditional timbers are Beech and Apple, but modern saw makers tend to use more exotics, whatever you choose make sure you have a piece large enough to orient the grain correctly, especially if you are planning an open handle. A piece 6" x 6" is a good start.
The first step is to thickness the timber to 7/8" you could go a little thicker (maybe 1") if you have long fingers or big hands and that feels better in your hand, but whatever you decide, this is going to be the final thickness of the handle.
The next step is to decide the layout, I have an acrylic template than allows you to position the template and see the grain direction, and any figure that might be worth highlighting. If you have a paper template, then trace the outline onto a piece of clear plastic and get the orientation right before glueing the paper onto the wood.
In this case I have a split that I need to avoid.
Decide the template position.
The next step is to mark the layout, I highlighted it with chalk, so it would be easier to see, a white marker would probably be better, there is a pencil line there but it doesn't show in the pictures too well.
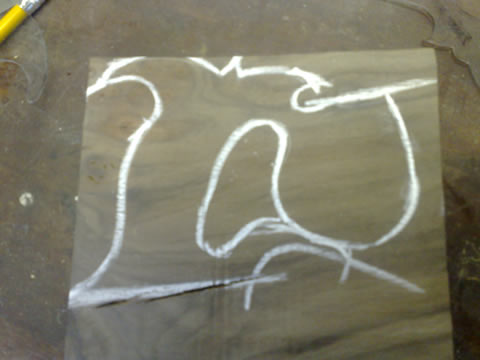
The next few steps are just to rough cut the outline. We start by drilling the corners out with forstner bits, mainly so we don't have to deal with sharp corners on the saw
Drill out the corners.
None of these holes are critical, but you can go as close as you like to the line without problems.
Then it's off to the bandsaw to kill a few electrons, you could use a scroll saw or a jig saw, or even a coping saw, of course the traditional turning saw is good as well.
Keep the cut close to the layout lines.
The center bit is best done with a coping saw.
Now we have a rough outline, we can start to refine the outline, DON'T get carried away and start any shaping, just stick to the outline for now. Use whatever you have, rasps, files, microplanes, bits of dowell with 80 grit paper glued to them work just as well. Take you time with this outlining, these are all final cuts, and work right up to the layout lines. Take care to blend any curves nice and smooth. Use a chisel to refine any sharp corners. Like the top nib, don't do any other shaping however we want the handle nice and flat for a bit longer yet, we have other stuff to do yet that is easier when it's nice and flat.
A good rasp is handy but, really, use whatever you have.
Microplanes cut fast and leave a pretty good finish.
For tighter curves a round file works just fine.
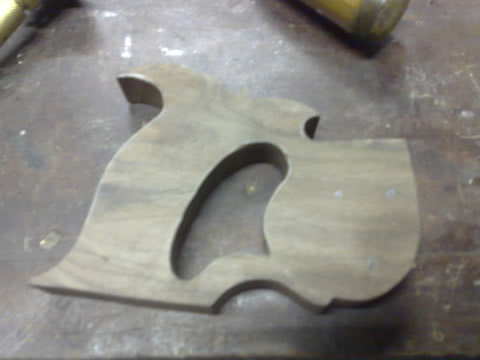
We already have our saw plate drilled and now carefully transfer the hole locations onto the handle blank, taking care to get the hang angle correct, if you mark the holes wrong in this step, there's no way back. So take you time and get it right.
Locate the saw screw holes
Take note of where the blade will finish in relation to the lambs tongue and the top beak. I have laid this one out to be in line with the brass back, but it doesn't have to be.
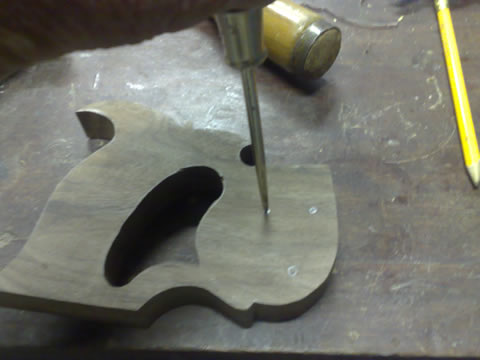
Mark the holes
Now mark the centers with an awl, and recheck against the saw plate that the holes are accurately centered.
Mark through to the other side
Now it's off to the drill press to kill a few more electrons, make sure your table is set up nice and square and then drill a small hole all the way through. I used a 1.5mm drill that was to hand, but 1/16 would do fine. The goal here is just simply to mark accurately through to the other side.
Once you've drilled through, recheck both sides against the saw plate to make sure you've got it right.
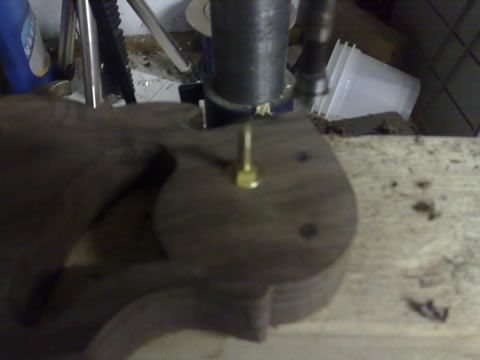
Now, change to a forstner bit that is the same diameter as the saw screws, I used 1/2" I thought I took a picture of drilling the recesses, but I can't find it. The only thing you are missing is the forstner bit has a line drawn with a marker pen showing the correct depth, drill just shy of the the full depth, and check the depth with a saw screw. Do both sides and take care to center the forstner bit on the small marker hole each time.
Now we have drilled the recesses both sides to just a little shy of the full depth.
Drill each hole to suit the shank if the saw screw, drill half way from each side taking care to center the drill in the center of the recess. It's important that this is done accurately and carefully. Get it wrong and it's back to square one....
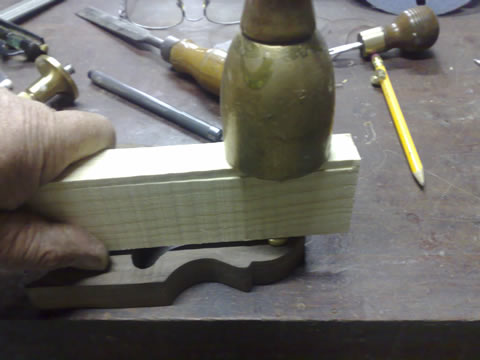
Now we have to cut the square recesses for the saw screws. Place a saw screw in the hole and tap firmly to mark the square section.
Now, with a 1/4" chisel chop out the recess for the square shank.
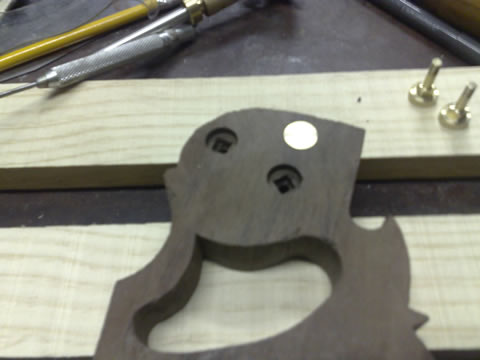
Test fit the saw screws and rework the square holes if needed.
The next bit is tricky, so take a break and relax the nerves....
Cutting the saw kerf must be done precisely, I have seen all different ways of doing it, the method shown here takes time and you must work slowly and keep checking constantly.
First we mark a center line
Mark from both sides to ensure we are centered, and carry the line all the way around the blank where the saw plate will be going.
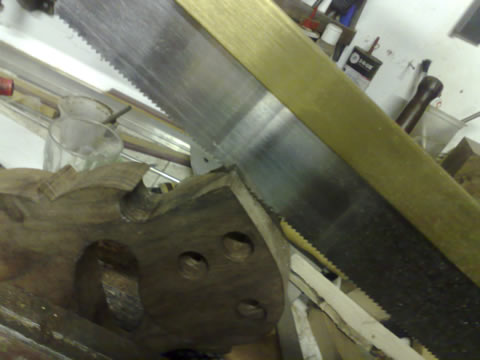
Start the cut on a corner, but don't cut too deep, maybe 1/8" or so, use a saw with a narrow kerf close to the thickness of the saw plate you are using.
Now gradually work the line around the handle taking care not to cut too deep and keep watching that the cut is nice and centered.
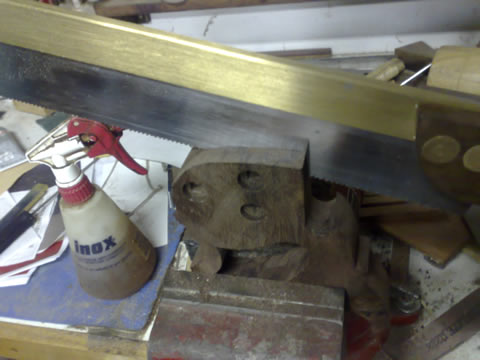
Gradually deepen the cut
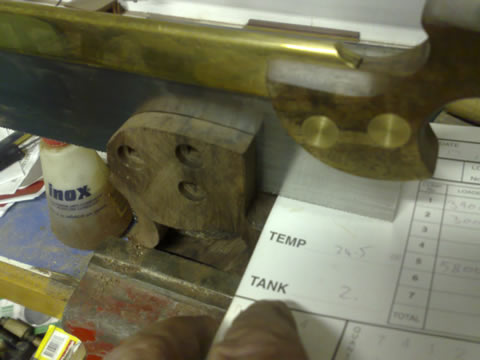
I ran out of depth with the dovetail saw, so swapped to another with a bit deeper saw plate. Still same kerf however.
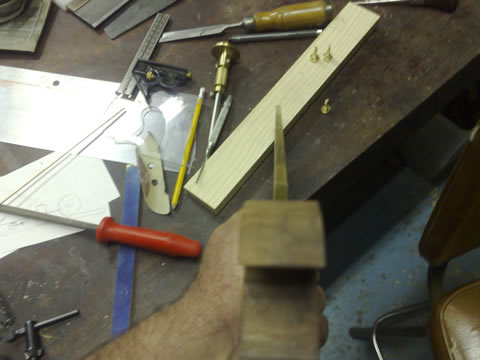
Test fit the blade and sight along the handle to make sure we are nice and straight..
Now breathe a sigh of relief, it gets easier from here on. Next task is to inlet the brass back.
Mark for inletting the brass.
Start by marking the cut we need to make directly from the back.
A sharp knife with a thin blade works best here, mark tight to the brass on both sides.
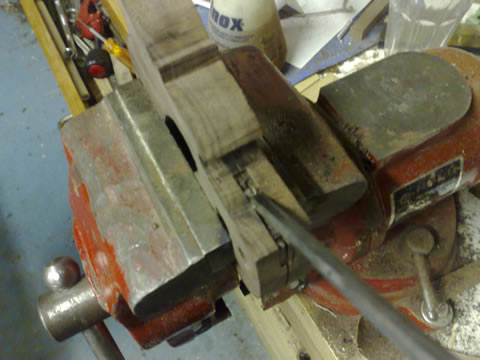
Now with a 1/4" chisel, or rather a chisel the same width as the back, work carefully staying off the lines and chop down.
You want to end up with a tight fit against the brass, so take care when working close to the edges
Keep test fitting and work slowly to make sure you don't over cut it.
Now we are ready for a trial assembly, to see if we got it nice and straight.
Use a tapered awl to line the plate up with the holes
All three screws should fit cleanly and sit just a little proud of the surface. They will pull down a bit when we tighten everything up later.
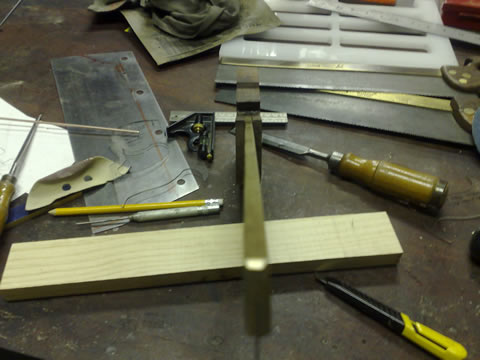
Recheck that everything is still nice and straight.
Now pull it all apart and we can start shaping the handle, (this is the fun part, right!)
Start by highlighting the areas we are going to shape
Note the line for the lambs tongue follows the curve of the boss.
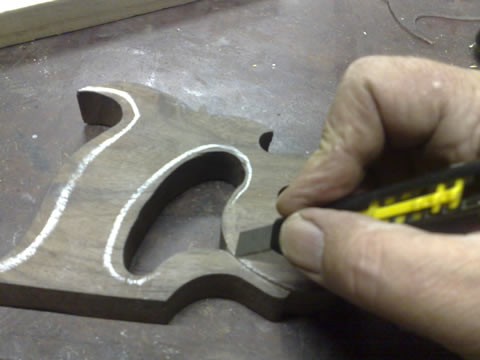
Use a sharp knife to define the line for the lambs tongue.
A gouge is more tolerant of grain direction.
Remove as much material using a chisel, or gouge if you have one. This is just to make for less work with the rasp later.
Just work to the lines and remove excess material
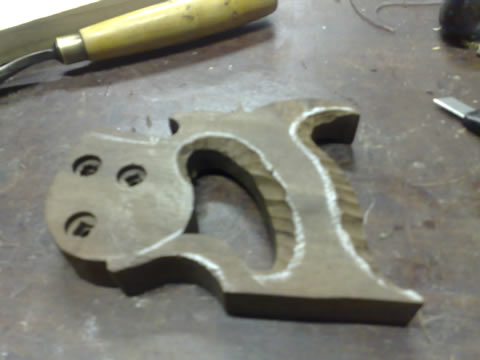
Define the rough shape, it's important that you keep eveything symetrical and don't over do it.
Now we can start refining the shape with a rasp.
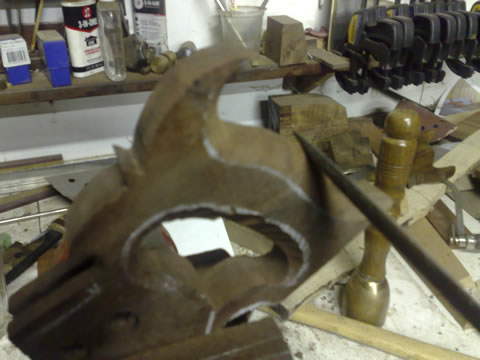
Gradually work the profile and keep smoothing out lumps and bumps and refining the shape.
Use a sharp knife or chisel to refine the sharper corners and details. When you are happy with the general shape, it's time to start smoothing.
I cut up sanding disks, they are stiff enough, that they don't follow the bumps too easily and course enough to cut reasonably fast, what we are trying to do is smooth the shape and remove rasp marks, (by replacing the rasp marks with sanding scratches!)
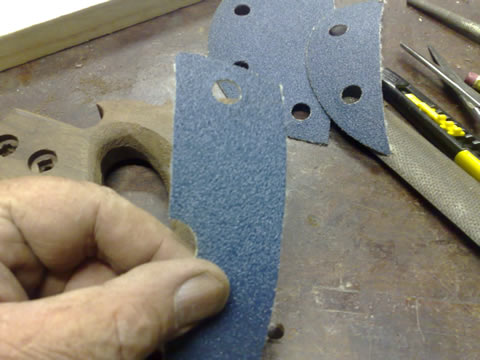
Gradually smooth the profile and remove the rasp marks
Work the inside curves by swiping the sandpaper around the curve, a bit hard to describe, sort of a rolling action, but dragging the sandpaper as you go.
As the smoothing progresses, apply a light coat of shellac and then move to 120 grit
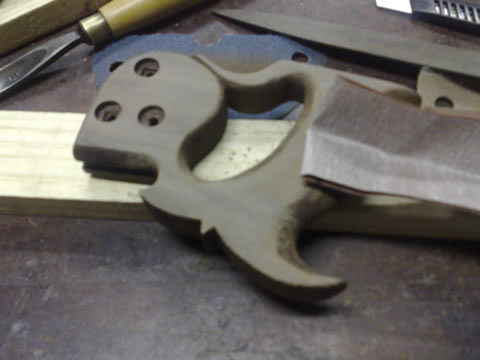
The shellac does a couple of things, initially it raises the grain, then later as more coats are applied it starts to fill the grain.
Move from 120 to 240, then finally 320 with light coats of shellac between grits. Keep looking for scratches and smoothing the curves.
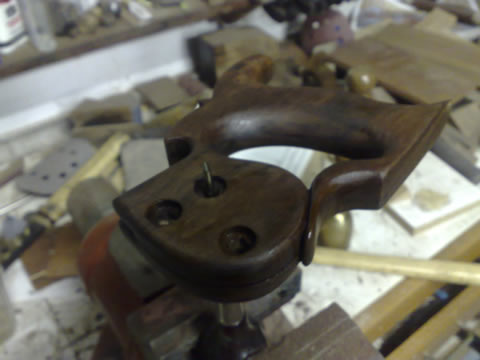
The final coat of shellac,
This is then lightly sanded with 320 one last time, and a light coat of UBEAUT wax applied and the it's off to the buffing wheel to be polished with an inch of it's life.
Then, here is the final assembly
That rounded look, is not the only option, after looking at it for a bit, I decided to go for that crisper more "manufactured" look with a shadow line..... so....
To get that look, you need to flatten the sides a little, you could just very carefully touch it up on a linisher, or a sheet of 220 grit on a flat surface works as well, but you then need to do a bit of refinishing..
The end result is something like this,
I could have polished the flat side bits a bit more, but you get the idea.
That's it, now get out of here, and have a go yourself.... it's easy I promise....
Regards
Ray
Introduction:
This is an article by IanW on various aspects of saw design, thoroughly enjoyable reading, and sure to provoke some discussion on hang angles canted blades and tooth profiles, and some examples of the beautiful saws Ian has made over the last few months. Many thanks to IanW for submitting this article, I hope he makes some more of those "Kenyon inspired" dovetail saws, very nice. ..Ray
Handles & teeth on small Backsaws
This is not a ‘how to’ on saw making; that has been well covered by others with way more experience than I have, but I would like to draw attention to a couple of points that, if they are mentioned at all by saw makers, it’s usually very briefly covered, as if anyone keen enough to tackle saw making would know already. I certainly don’t claim any great wisdom, and wish to provoke some discussion rather than lay down any laws. The topics I’m referring to are, angle of the grip (with respect to the line of the teeth) and choosing tooth pitch & profile. It’s interesting to see those old adverts from 100 years ago when saws of every conceivable size could be supplied with any number of teeth per inch the buyer desired. At first that seemed a bit odd to me, I thought there should be well-established rules for what is “best”, given the number of skilled people wielding them on a daily basis. However, that is precisely why, I think, there were no simple rules. When you consider that saws were used by people of different skill levels, for many different purposes, in many different woods, it’s hardly surprising that practiced hands would find what suited them best & want tools that delivered their needs.
I’ll start with grip angles, because that’s the simpler topic & I think I have figured that one out to my own satisfaction. A long time ago, I remade the handle for a new 8” brass-backed Tyzack saw. The thing that came with it was hardly worth the dignity of the name ‘handle’ – it was crude, ugly & uncomfortable to hold. My replacement was a copy of one I saw on an old saw belonging to someone else. I gave it no more thought at the time other than I liked the look of it & it seemed comfortable in my fist. That little saw had very fine teeth & I used it for general crosscutting of small pieces, but after reading an article in FWW, I had it recut to a 15tpi rip pattern for dovetailing. I was amazed at the change in character of that saw – it went from a so-so tool to a very accurate and useable instrument. My clumsy efforts at sharpening meant the saw varied a lot in its cutting action, but gradually, I learnt how to keep a proper profile on the teeth, and just as importantly use a very fine set. Even though I subsequently acquired several small backsaws, I always reached for this one to cut dovetails, even when its state of sharpness was a bit dodgy, and it’s only recently that I realised why. It’s because the grip angle is just right for holding the saw comfortably for this process. Intuitively, I arrange the position of the piece to be cut at a height above the bench so that my forearm is more or less parallel to the bench. In this position, the saw sits easily, with my wrist at a comfortable & natural angle, which allows me to start a cut at the correct angle to follow a line perfectly from start to finish. This is important because the minimal set on this saw means it can’t be ‘steered’, you have to begin straight & remain straight for the rest of the cut.
Fig. 1. On the left is the rehandled Tyzack held with my forearm parallel to the bench. With wrist in a comfortable position, the tooth line is more or less square to the bench top. The angle between tooth line & the centre line of the grip is about 65 degrees.
The next saw I modified was a cheap 18tpi backsaw bought new for the princely sum of $5 (though that would be more like $30 now). This was a surprisingly good little saw, but its thin steel back gave it little heft, and the red-painted knife handle was hardly a work of art. I saw a picture of Duncan Phyfe’s tool chest one day, & noticed these attractive pistol-grip handles on his small saws, so on a whim, I made a new handle from a scrap of figured walnut & stuck it on. I paid little attention to the angle of the grip – just made the handle to look like what I’d seen, & stuck it on (this was also when I discovered how difficult it is to drill saw plate with an ordinary drill bit). I failed to appreciate that the butt of the grip would hang down about 20mm below the line of the teeth until it was too late. It meant the saw was a bit awkward to use on a bench hook, but for nipping off corners of tails & small tenons held in a vise, it was fine, & has seen lots of use.
Fig. 2. The modified 18tpi saw with added brass back and pistol grip handle – note how the grip extends well below the tooth line.
The next raising of my awareness of grip angles came when I rehandled another old clunker. This was my closest approach so far to saw making – I also fitted a new brass back at the same time. I used a handle template I got from somewhere on the web – can’t remember where, but this one has been around for a very long time (Ray has it on his website now, I noticed). So I carefully tarted up my new handle, stuck it on, & took a test drive. Another revelation – this handle felt just right when crosscutting on my bench hook. A quick comparison with my other saws shows the difference – the grip on this one makes an angle of about 52 degrees with the line of the teeth – much more “kicked up” than the other saws mentioned, and keeps my wrist at a very comfortable angle when my forearm is angled down toward the bench, as it is in this operation. This was also the tipping point in my saw making career – Ray saw it when I put it up on a bulletin-board, and encouraged me to make a saw from scratch. He even most generously provided me with a good-sized chunk of saw plate – thanks Ray, but you don’t know what you started!
So my conclusion is, grips at different angles suit different operations – hardly rocket science, but I simply hadn’t thought much about it til then. I do most sawing with my forearm either parallel to the bench, in which case a grip that makes an angle of about 60-65 degrees to the tooth line is ideal for me, or with my forearm angled down to the bench surface, in which case a grip angled about 50-55 degrees to the tooth line works best. Doesn’t seem like a lot, but it makes a big difference to comfort. And here I can throw a match into the debate about canted blades– one effect of this is that when the handle is fitted with the fillets parallel to the back, as is usual, it throws the grip up slightly, giving it more clearance when used on a bench hook, as I found when I made my own copy of the Kenyon saw that was being touted around a while ago. But even larger saws, which have plenty of handle clearance, were canted, so I don’t seriously think there was a reason other than fashion.
Fig 3. 220mm “Kenyon” style saw, 15tpi, with canted back. The grip makes an angle of 55 degrees with the tooth line, and is a good compromise for cutting at a range of arm heights. It projects slightly below the tooth line, but is ok for most cutting operations on a bench hook.
Now, onto more complicated and fraught issues – the tooth pitch and their preferred profiles. There is really no ‘right’ answer to these questions, of course – witness the endless variety you find in old backsaws. Skilled saw sharpeners like my old dad had no compunction in recutting & re-shaping teeth to make a saw more fit for some purpose, so I’ll bet it was a fairly common practice way back...
Now I was taught by my manual-training teacher at school that you should have a minimum of 4 to 5 teeth in the cut. I’ve seen other recommendations, but they are all pretty similar, and the idea is to have enough teeth resting on substrate that they don’t bite too hard & jam, or worse, rip the top off a tooth. As in just about every facet of life, the ideal is rarely attainable & we generally have more teeth than that in a cut, which means waste clearance & cutting is less efficient than it could be. In the sort of general joinery I do, & the typical width of saw cuts, I have found 12 & 15 tpi to be the most useful pitches for small saws. Until a few years ago, I tended to go for finer teeth, but now that I’m a much better sharpener, I realise that my preference for finer teeth was because my terrible sharpening didn’t create as much variation in tooth heights, which gave the illusion of smoother cuts. But now I can sharpen a saw so that the teeth are very much closer to even, I find a coarser pitch can cut just as smoothly, and much more quickly in most situations. The thinnest sections I would normally cut would be small drawer sides, at around 10mm, so that a 15tpi saw will have at least 6 or 7 teeth in the cut. Thicker pieces will support many more teeth, so to cut something over about 30mm wide, I would pick up one of my bigger 12tpi carcase saws. Although it would cut a wider kerf, it will cut more quickly and accurately in the longer cut.
Tooth profiles I’ve left to last. Here I found a bit of a surprise when I mucked about with a few different angles. I started out adhering to the recommended rake angles for crosscut & rip, but over time have come round to putting 5 degrees of rake on both. This makes ripsaws easier to start & smoother cutting, and gives crosscuts a bit more ‘bite’ so that they can be used for shallow ripping. I don’t find it makes the crosscuts any less smooth in their cutting action – as long as I give them about 15 to maybe 20 degrees of fleam, they seem to cut cleanly. With only one rake angle to set up & maintain I seem to be able to be more consistent, which is important for someone who doesn’t file saws every day.
So those are my thoughts after 50 years of wielding saws, but only a short time really thinking seriously about what they do. They are, naturally, a reflection of the types of woods & cuts I make with my backsaws (more traditional cabinet woods, not the really hard stuff). I haven’t tried to fool around with any larger handsaws just yet – for now I’m content to follow the profiles they came with.
And one last observation – for those whose eyesight is as chronologically challenged as mine, one of those 5x headband magnifiers is a godsend – it’s a bit of a nuisance having your snout so close to the action, but it’s so good to be able to see clearly what’s happening to those little teeth as you file!
For the record, here is my current stable of backsaws. All bar one recently made, but replacing similar saws, so although I haven’t had most of these saws more than 6 months, I have used the same lineup for some years now. With this lot, I rarely wish for anything more – they do everything I require very well.
Fig. 4. From top to bottom:
1. A 300mm 12 tpi rip, from 0.5mm plate. A fast-cutting saw with a very fine kerf & a bit of an enthusiast’s tool as it takes some practice to control due to the minimal set.
2. My most recently-made D9 style, 310mm, 12 tpi xcut. This is made from 0.75mm plate, and has the first 25mm from the toe filed at ~15tpi – easy to start & cuts nicely.
3. A very comfy 250mm 15tpi xcut. This has the 52 degree “compromise” handle that makes it a very good little all-rounder.
4. The oldest & only commercial saw left – a 200mm, 15tpi rip. Formerly my ‘favourite’ dovetailer, but rapidly being squeezed out by the next saw....
5. This is a little beauty! My “Kenyon” style, 15tpi “semi-xcut” which crosscuts & rips thin stock with equal facility. The 55 degree grip is a very comfortable compromise for most bench work.
6. A somewhat whimsical 150mm 18tpi xcut – handy for small jobs like nipping off an end on lathe work or anywhere where a fine, slow cut is called for.
IanW June 2009
Page 2 of 2